Pharmaceutical Plants & Equipment
Mixer for Solids – Dry & Wet
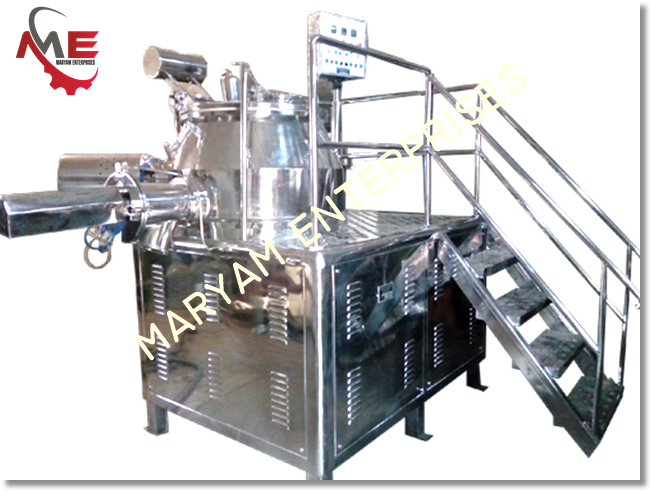
HIGH SHEAR MIXER GRANULATOR-HSMG / RAPID MIXER GRANULATOR – RMG
MARYAM ENTERPRISES is a leading and well known manufacturer of High Shear Mixer Granulator, used for process of fast dry & wet mixing, homogenizing, humidifying and granulating of the powder in Pharmaceutical, Chemical, Cosmetic, Food, Plastic, General Mixing Industries.
High Shear Mixer Granulator series is characterized by the compact construction, modern design and all the user and maintenance friendly attributes which form the ergonomics design aspects are essential for a wide range of application.
The High Shear Mixer Granulator performs dry mixing & wet granulating by basic design of the special four arm of the mixing impeller and sequences of the mixing process in the cylindrical mixing drum with rounded connection to the base plate, achieve another special effect. The mixing process runs without varying pressure zone in the volume of mixing product.
Separately driven multiple choppers can effectively intensify the mixing result in particular when liquid or paste components are added. During humidifying and granulating process of the products the chopper controls and regulates the granular spectrum and structure of the granules according to the product, chopper shape and time. The HSMG system requires only small quantities of granulating liquid or pastes to obtain the required granulate structure. This reduces the amount of drying energy required.
Salient Features:
- High speed mixing & granulating
- Design is cGMP – Current Good Manufacturing Practices compliance
- All Product contact parts AISI 316 & non contact parts AISI 304.
- Automated maxing and granulating process in single bowl.
- High Precision mixing and granulation with Short Batch Time, Problem free Cleaning and Residue Free Discharge.
- Unique design with four arm mixing impeller with blade angle to pushing product radically outward.
- Chopper blade designed to cuts lumps and make granules.
- Dual speed mixing impeller for mixing and intensify chopper for granulating.
- Flush fitting discharge plug is electro pneumatically operated.
- Air pursing for seal for both shafts.
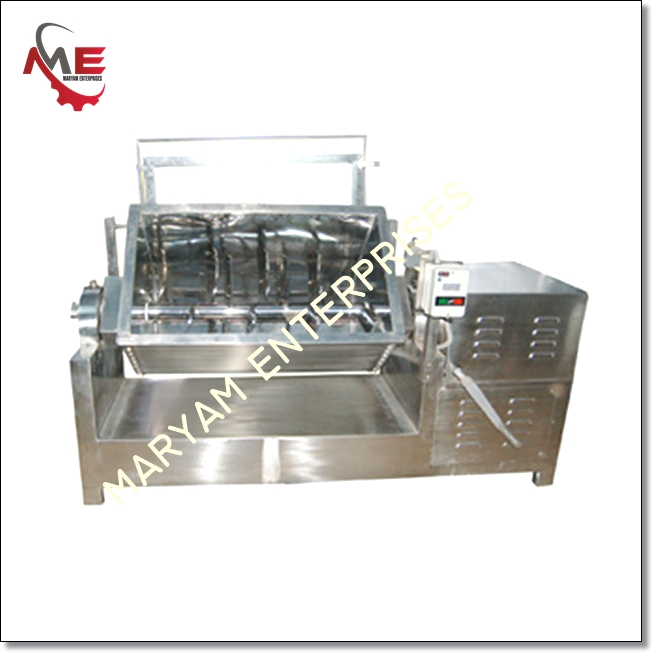
MASS MIXER
MARYAM ENTERPRISES is a leading and well known manufacturer of Mass Mixer, is designed for uniformly mixing of dry and wet material and especially suitable for powder of Pharmaceuticals, Food, Herbals, Agro Chemicals & Chemicals.
The mass mixer consists of a rigid fabricated structure motor, gear box, mixing drum, stirrer and tilting device. Specially designed self adjusting sealing arrangement of unique design is provided to ensure that no black particle enters into the mixing drum. The material under mixing process can be monitoring through acrylic dust cover and its controls dusting and contamination. The tilting device is provided to make easy the unloading of the material and easy cleaning of the mixing drum.
Salient Features:
- Ideal For Mixing Dry & Wet Material.
- Paddles Type Blades So Arranged On The Shaft To Give Through Uniform Mixing Of Thick Heavy Material.
- The Drive System Is Through Suitable Worm Gear And Motor.
- Provision For Tilting Arrangement , Reversible Switch And Safety Lock-switch To Stop The Mixer As Soon The Cover Is Opened.
- PTFE Gland Mechanism Provided at Shaft ends to Prevent Inner Leakage.
- The Mass Mixer Is Also Provided With A Lever With Hand Wheel To Accomplish Tilting Manually.
Salient Features: (Flame Proof Electric.)
MODEL | PMM-50 | PMM-100 | PMM-150 | PMM-200 | PMM-300 | PMM-500 |
Capacity in Kg | 50 | 100 | 150 | 200 | 300 | 500 |
Brim Volume in Liter. | 100 | 200 | 300 | 400 | 600 | 1000 |
Working Volume in Liter. | 80 | 160 | 240 | 320 | 580 | 800 |
Stirrer RPM | 30 | 30 | 30 | 30 | 30 | 30 |
Electric Motor hp / kw | 3 / 2.25 | 5 / 3.75 | 7.5 / 5.6 | 7.5 / 5.6 | 10 / 7.5 | 15/11.25 |
PADDLE MIXER BLENDER
MARYAM ENTERPRISES is a leading and well known manufacturer of Ribbon blender mixer, is used for uniformly dry mixing and blending applications in the pharmaceutical, chemical, cosmetic, food, pesticides, detergents, and plastics industries. The Ribbon Blender comprises of a U-shaped horizontal trough, specially designed Double Helical Ribbon Agitator, rigid fabricated structure motor, gear box.
In operation, material is filled to the top of the outer ribbon. The shaft rotates at relatively low speed and the moving ribbons push the material back and forth mixing it. The outer ribbon rotation displaces the material from the ends to the center while the inner ribbon rotations move the material from the center to the ends. This counter-current action results in homogeneous blending. Mixing is achieved in 15 to 20 minutes with 90 to 95 % or better homogeneity. The bottom discharge provided for unloading of the material and easy cleaning of the mixing drum. Specially designed self adjusting sealing arrangement of unique design is provided to ensure that no black particle enters into the mixing drum.
Salient Features:
- Design is cGMP – Current Good Manufacturing Practices compliance.
- All contact parts AISI 316 & non contact parts AISI 304.
- High mixing technology provides the ideal environment for effectively mixing a wide distribution of particle size and bulk densities without segregation.
- Available in Capacity 50 kg to 4000 kg. model
- Fluidization assures homogeneous mixes independent of large range of particle size, shape or density
- It has ability to mix in approximately 30-60 seconds for dry applications so increased production capacity and consumed energy is potentially 80% less for any given batch.
- Paddle agitator for center discharge.
- Inner & outer paddles on the triple action multi-zone rotor.
- High Speed stirrer up to 60 RPM.
- Extremely gentle with fragile ingredients
- Minimal heat generated due to internal friction & High particle movement
- Fast, even liquid addition and coating by spraying system.
- Ideal for agglomerating and No over mixing
- Direct drive gear box with motor.
RIBBON MIXER BLENDER
MARYAM ENTERPRISES is a leading and well known manufacturer of Ribbon blender mixer, is used for uniformly dry mixing and blending applications in the pharmaceutical, chemical, cosmetic, food, pesticides, detergents, and plastics industries. The Ribbon Blender comprises of a U-shaped horizontal trough, specially designed Double Helical Ribbon Agitator, rigid fabricated structure motor, gear box.
In operation, material is filled to the top of the outer ribbon. The shaft rotates at relatively low speed and the moving ribbons push the material back and forth mixing it. The outer ribbon rotation displaces the material from the ends to the center while the inner ribbon rotations move the material from the center to the ends. This counter-current action results in homogeneous blending. Mixing is achieved in 15 to 20 minutes with 90 to 95 % or better homogeneity. The bottom discharge provided for unloading of the material and easy cleaning of the mixing drum. Specially designed self adjusting sealing arrangement of unique design is provided to ensure that no black particle enters into the mixing drum.
Salient Features:
- Available in Capacity 50 kg to 5000 kg. model.
- Design is cGMP – Current Good Manufacturing Practices compliance.
- All contact parts AISI 316 & non contact parts AISI 304.
- Uniform dry maxing process.
- The shape of container and mixing stirrer gives sufficient continuous movement to the powder / granules result in good quality. Minor ingredients are dispersed homogeneously without the need for pre-mixing
- Double or triple action with blending occurring in the small voided areas immediately behind the blending ribbons.
- The interlocked acrylic covers of product container, enclosed drive& Overloads relay protection.
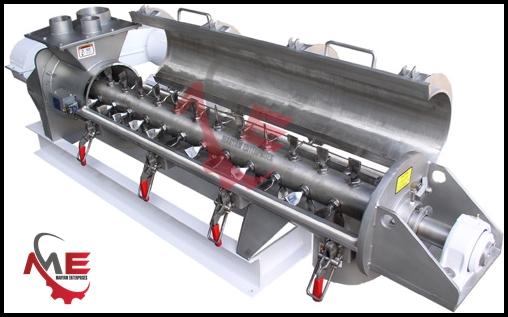
CONTINUOUS MIXER BLENDER SYSTEM: SIMPLEX MIXER
MARYAM ENTERPRISES is a leading and well known manufacturer of Single Shaft Continuous Paddle Mixer Blender, is designed for uniformly wet & dry mixing and blending technology provides the ideal environment for effectively optimum mixing a wide distribution of particle size and bulk densities without segregation of powder, granular, short fibered, moist solids and liquids together with pasty substances up to and including highly viscous masses in the pharmaceutical, chemical, herbal, cosmetic, food, pesticides, detergents, and plastics industries. The Mixer produces high quality intermediate and end product with homogeneity. Extremely fragile products are handled very gently. Micro ingredients are accurately mixed.
- Dry Solid Blending
- Solid and liquid blends
- Coating
- Granulation
- Flavoring
- Premixing for extrusion
Single shaft continuous mixer make material rotate along with main shaft. Mixer agitator break material and mix material in the mean time. It is suitable for mixer material with different density, size, etc. Continuous mixer depend on continuous and proportioned feeding, so should be combined with feeding system.
During mixing process fluidization assures homogeneous mixes independent of large range of particle size, shape or density. The paddles are positioned to move the material in lateral directions as well as radically. The mixer consists of a rigid fabricated structure motor, gear box, mixing U-shaped horizontal drum and peddle type stirrer.
Salient Features:
- High mixing technology provides the ideal environment for effectively mixing a wide distribution of particle size and bulk densities without segregation.
- Fluidization assures homogeneous mixes independent of large range of particle size, shape or density
- Extremely gentle with fragile ingredients
- Fast, even liquid addition and coating by spraying system.
- Ideal for agglomerating and No over mixing
- Easy, fast and complete discharge.
- Low space requirements.
- Available in Capacity 250 to 75,000 Liter per hour.
- Design is cGMP – Current Good Manufacturing Practices compliance
- All Product contact parts AISI 316/ 316L & non contact parts AISI 304.
- Product container trough types : “U” shape OR Round
- Direct drive gear box with motor.
- Shaft seal both side with stuffing box with food grade seal.
PLANETARY POWDER MIXER
MARYAM ENTERPRISES is a leading and well known manufacturer of Planetary Mixer, is ideal for mixing of wet/dry powder materials. It has a homogeneous mixing action i.e. emulsions and semisolid. It integrates mixing, vacuuming, heating, cooling and homogenizing functions into single machine, resulting in a considerably reduction in cycle time.
The basis of mixing system of Planetary Mixer is a combination of planetary- rotating paddle agitator. 2 Nos. Anchor type agitator with cross baffles rotates in anti-clockwise direction with planetary motion in there axis. While paddle revolves in clockwise direction with planetary action, generating a disturbance in the normally circular flow pattern and dampen vortex formation. The mixing blade and planetary action having dual speed. In addition, adjustable scrapers are utilized to prevent the build-up of a stagnant film between the agitator and the vessel, and assure efficient heat transfer to product during heating and cooling steps. The speed of the agitator and the counter paddle can be varied separately.
The Product container is castor wheel mounted for easy load and unload to the machine. The top mixing blade assembly is motorized up and down during container loading and unloading. The mixing container is jacketed for heating / cooling and completely enclosed. The product container can be designed to operate under vacuum; mixing can then be performed without entrainment of air. Top lid of the product container having charging pot for binder adding, eye glass window and light glass.
Salient Features:
- Designed strictly compliance with the stipulation of cGMP
- Product contact parts AISI 316 Quality and Non contact parts S.S.394 Quality.
- Machine compact in designed single base structure to for simplicity in mounting.
- 2 Nos. Anchor blade with planetary rotation for extremely efficient shearing force.
- Top lid is mounted with motorized lifting device.
- Product container is castor wheel mounted for easy load and unload to the machine.
- Rigid drive with planetary gear and reduction gear box
- Dual speed motor for slow and fast mixing action.
- Scrapper is made from Teflon.
BLENDER
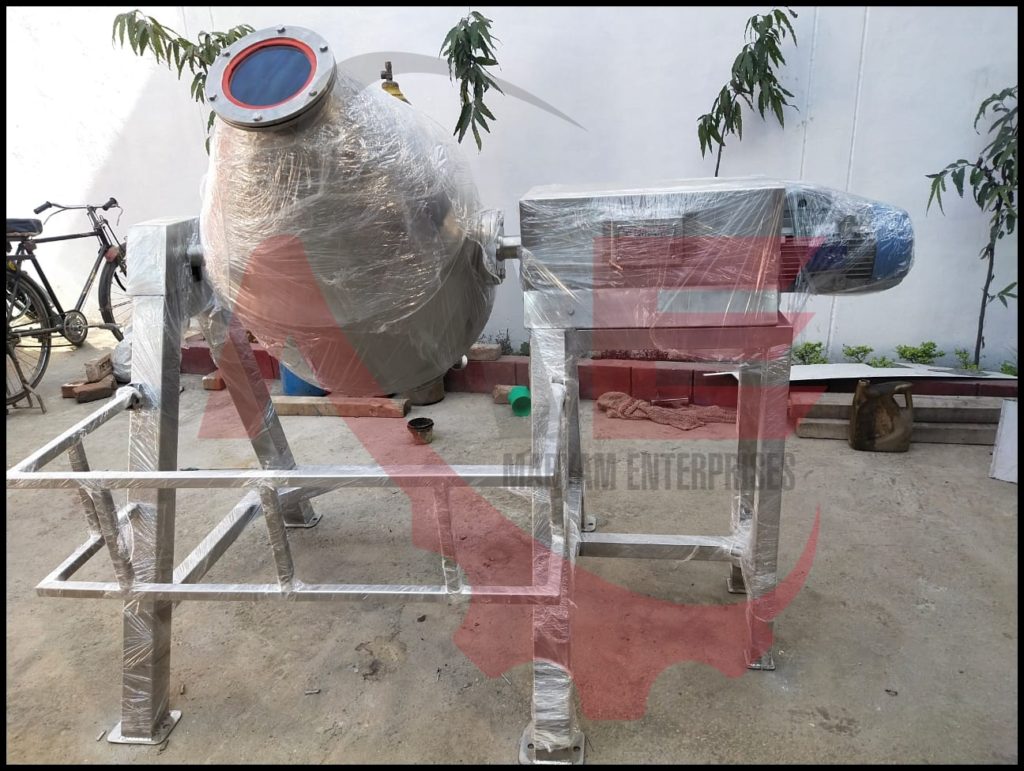
DOUBLE CONE BLENDER
MARYAM ENTERPRISES is a leading and well known manufacturer of Double shape blenders, have long two corner of product container for more rubbing and tumbler effect to the material for fast and homogenizing mixing. It can perform homogenously dry mixing of free flowing powders, granules requiring low shearing force, Mixing and Blending of particles with rapid intermixing of particles irrespective of varying specific gravities. The material is loaded into the double cone blender drum. The double blender is tumbles the material in the container and spread out. The mixing is achieved in 5 to 15 minutes with better homogeneity.
Salient Features:
- Design is cGMP – Current Good Manufacturing Practices compliance
- All Product contact parts AISI 316 & non contact parts AISI 304.
- Double Cone shape product container for Ideal dry mixer for lubrication of granules and homogenization mixing of multiple batches in to single batch.
- Available Capacity model in octagonal blender 25 kg to 2500 kg batch size..
- Enclosed rigid drive with reduction gear box and motor.
- “A” type rigid structure of the machine with two sides resting of product container.
- Product container having discharge with butterfly valve and man hole.
- Charging hole with hinged lid with seal for charging and cleaning.
- The product container rotates on sped 8 RPM.
- Safety reeling provided for rotating area of product container.
- Fixed baffles provided for lumps braking.
- Electric controls panel with cycle time.
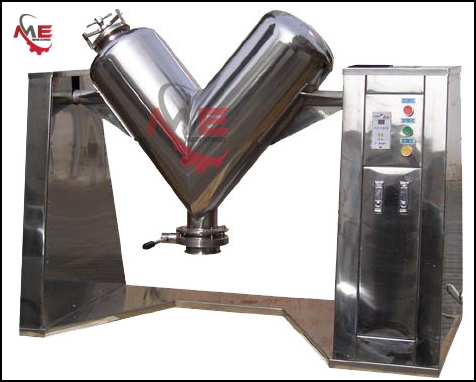
“V” SHAPE MIXER BLENDER
MARYAM ENTERPRISES is a leading and well known manufacturer of “V” Shape Blenders, are used for mixing, lubricating and blending in Pharmaceutical, Nutraceutical, Food, Chemical, cosmetics, ceramics, pesticide, plastics and other Allied industries
The product containers have “V” shape so it crated continuously split and recombines of the material with more tumbler and friction effect to the material for fast and homogenizing mixing. It can perform homogenously dry mixing of free flowing powders, granules requiring low shearing force, Mixing and Blending of particles with rapid intermixing of particles irrespective of varying specific gravities. The material is loaded into the ‘V” shape blender drum. The ‘V” shape blender is tumbles the material in the container and spread out. The mixing is achieved in 5 to 15 minutes with better homogeneity.
Salient Features:
- Design is cGMP – Current Good Manufacturing Practices compliance
- All Product contact parts AISI 316/ 316L & non contact parts AISI 304.
- ‘V’ shape product container for Ideal dry mixer for lubrication of granules and homogenization mixing of multiple batches in to single batch.
- Available Capacity model in octagonal blender 25 kg to 2500 kg batch size..
- Enclosed rigid drive with reduction gear box and motor.
- “A” type rigid structure of the machine with two sides resting of product container.
- Product container having discharge with butterfly valve and man hole.
- 2 Nos. Charging hole with hinged lid with seal for charging and cleaning.
- Safety reeling provided for rotating area of product container.
- Fixed baffles provided for lumps braking.
- Electric controls panel with cycle time.
Optional Features:
- Loading & Unloading by Product container with Jacking trolley.
- Vacuum conveying system.
- Bin loading by hydraulic hoist.
- Interchangeable with different capacity ‘V” shape product container.
- Rotary Intensifier with AC variable drive.
- AC Frequency variable drive for product container.
- PLC Controls with HMI touch screen,
- Flame proof motor and Push Button station.
- Inline milling and loading with vacuum transfer systems.
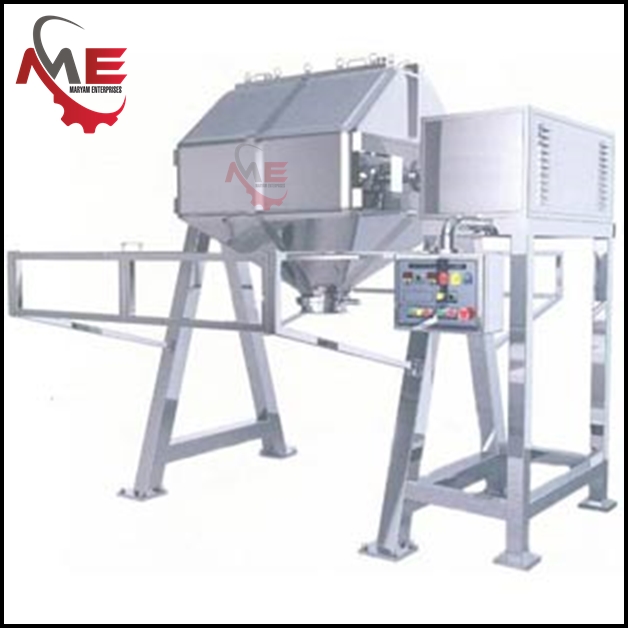
OCTAGONAL BLENDER
MARYAM ENTERPRISES is a leading and well known manufacturer of octagonal shape blenders, have six corner of product container for more tumbler effect to the material for fast and homogenizing mixing. It can perform homogenously dry mixing of free flowing powders, granules requiring low shearing force, Mixing and Blending of particles with rapid intermixing of particles irrespective of varying specific gravities. The material is loaded into the blender drum. The octagonal blender is tumbles the material in the container and spread out. The mixing is achieved in 5 to 15 minutes with better homogeneity.
Salient Features:
- Design is cGMP – Current Good Manufacturing Practices compliance
- All Product contact parts AISI 316 & non contact parts AISI 304.
- Octagonal shape product container for Ideal dry mixer for lubrication of granules and homogenization mixing of multiple batches in to single batch.
- Available Capacity model in octagonal blender 25 kg to 5000 kg batch size.
- Enclosed rigid drive with reduction gear box and motor.
- “A” type rigid structure of the machine with two sides resting of product container.
- Product container having discharge with butterfly valve and man hole.
- Charging hole with hinged lid with seal for charging and cleaning.
- Safety reeling provided for rotating area of product container.
- Fixed baffles provided for lumps braking.
- Electric controls panel with cycle time.
Optional Features: (Charging Option)
- Loading & Unloading by Product container with Jacking trolley.
- Vacuum conveying system.
- Bin loading by hydraulic hoist.
- Rotary intensifier with AC variable drive.
- Variable speed for product container by VFD.
- PLC Controls with HMI touch screen,
- Flame proof motor and Push Button station.
- Inline milling and loading with vacuum transfer systems.
DRYER
FLUID BED DRYER
MARYAM ENTERPRISES is a leading and well known manufacturer of Fluid Bed Dryer, have a bed of solid particles which are fluidized by passing a stream of air upward through a specially designed perforated sheet. The upward velocity of air is so maintained so as to slightly lift the solid particles and set them in motion. This motion can be utilized to bring about mixing as well as forward movement of the solids particles. The air is heated and the process hot air evaporates the fluid and dries the solids. Fines get agglomerated to larger granules particles thus providing large size
The machine is designed with correct volume of bowl, air velocity, direction and the temperature of the clean inlet air is maintained throughout the fluidization, retarding, and expansion chambers, filtration area, pitch of the perforations of the plate at the bottom of product container, the leak-proof fluidization space by proper sealing, material of the filters and process controls with electrical & pneumatically.
The uniform drying is achieved by exposing the full surface of every particles of the solid mass to the incoming high velocity hot air.
Option for the process parameters are controlled by using latest PLC controls with HMI touch screen thus making equipment operationally safe and eliminating the possibility of human error. The process consistency with batch records is maintained for every batch every time.
The equipment can be inbuilt CIP system gives a thoroughly cleaned equipment for every batch eliminating contamination of subsequent batches.
Salient Features:
- Design is cGMP – Current Good Manufacturing Practices compliance.
- All contact parts AISI 316 & non contact parts AISI 304.
- Single piece construction with Integrated retarding expansion chamber cum filter bag housing
- Batch type dryer with available capacity 30 kg to 500 kg. Batch size
- Pneumatic Sealing of Filter Bag and Product container by inflatable silicon rubber tube.
- Inlet Air handler with Air Filter- Micro, HEPA and Heat Exchanger Steam or Electric.
- Exhaust air blower with dynamic balance fan.
- Built in Explosion vents and isolation valve protect equipment.
- Automatic Temperature controls for Inlet Air and Process cycle time controls.
- Washable filter media, FDA approved.
- Auto pneumatic filter bag shacking system.
- Sampling pot on product container.
- Electric and Pneumatic controls panel.
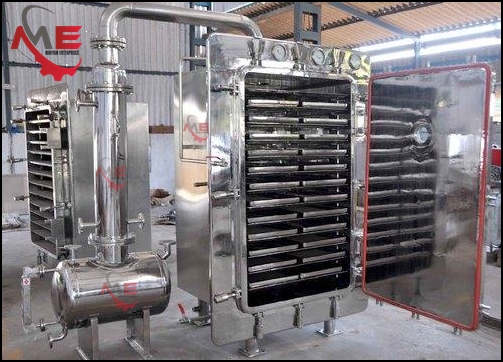
TRAY DRYER
MARYAM ENTERPRISES is a leading and well known manufacturer of Tray Drying Ovens, are used for drying of pharmaceutical powders, granules, Pigments, Food, Bakery, Electrodes, Chemical, and Plastic etc in an effective and economical way by hot air re-circulation.
Tray dryer is an enclosed insulated chamber in which trays are placed on top of each other. Heat transfer is done by circulation of hot air by electric heaters or any other heating media. Blower fans are installed inside to ensure proper circulation and transfer of heat.
Salient Features:
- Available in 24, 48, 96 & 192 Trays.
- Design is cGMP – Current Good Manufacturing Practices compliance.
- All contact parts AISI 316/304 & non contact parts AISI 304/ M.S. with painted.
- Highly effective uniform air re-circulating system by low speed fan.
- Inlet air filter and damper at inlet and exhaust air damper for air flow controls.
- Controls panel with Digital temperature controller and process timer controller.
- Mobile trolleys are provided which are used to load and unload the trays into the dryer.
Optional Features:
- Heating system Electrical / Steam / Gas Heating.
- Separate Inlet AHU with HEPA Filtration.
- Perforated tray
- Standard Painted Model.
- Safety Features :
- Automatic Temperature & controls, Process cycle controls.
- Overload relay Protection and Emergency stop button.
Technical Specifications:
MODEL | PTD – 24 | PTD – 48 | PTD – 96 | PTD – 192 |
Number of Trays | 24 Trays | 48 Trays | 96 Trays | 96 Trays |
Loading capacity | 60 kg. | 120 kg | 240 kg. | 480 kg. |
Blower motor Hp | 1 HP | 1 HP | 1 HP X 2 Nos | 1 HP X 4 Nos |
Electrical Heating Load for 100°C | 6 kW | 9 kW | 15 kW | 36 kW |
No. of Trolleys | Rack system | One | Two | Four |
Tray Size in cm | 80 X 40 X 3 | 80 X 40 X 3 | 80 X 40 X 3 | 80 X 40 X 3 |
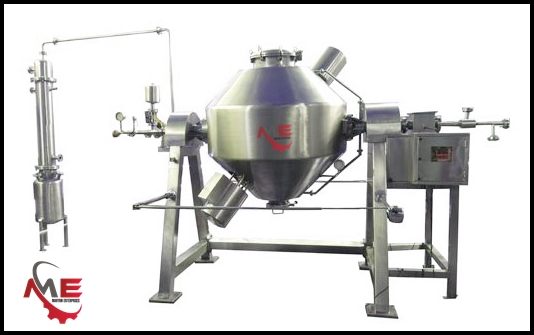
RCVD (ROTOCONE VACUUM DRYER)
MARYAM ENTERPRISES is a leading and well known manufacturer of Double Cone Rotary Vacuum Drye,r is suitable for drying the material which can not operate at low Temperature easily oxidized, poisonous in nature. The Double Cone Rotating Vacuum Drying Equipment is a new drier that integrates mixing and drying in the one body and equips with condenser and vacuum pump. Therefore the vacuum drier is formed. The drier is advanced in design, simple in inner structure, easy for cleaning, to discharge all raw material, convenient in operation and improving work environment. Meanwhile raw material is rotating accompanying with the rotating of container; raw materials cannot be accumulated onto the wall of container, so it has high efficiency heat transfer and high speed drying which save energy. Raw materials are dried uniformly and have good quality at low temperature. It can widely apply to dry raw materials of pharmaceuticals, chemical, Pesticides, foodstuff , dyestuff and so on industries. The equipment is in conformity with the requirements of “GMP”. If the solvent does not recover, the condenser may be not used.
- Material that cannot undertake high temperature.
- Material that is easy to oxidize.
- Material that do not permit to destruct.
- To recover material with residual volatile.
- Material with vigorous irritative and toxicity
The Double Cone Rotary Vacuum Dryer consists of a jacketed double conical shell rotating around 6 RPM with under the state of vacuum inside the shell, pass steam or hot water in to jacket for heating. The large heating surface area presented by the internals of the cone ensures uniform drying of the product, as the product gently tumbles while the cone rotates slowly. The vaporized steam can be pumped out through vacuum exhaust pipe when the damp raw material absorbed heat. The diffusive action induced by the tumbling cone constantly presents a fresh layer to come into contact with the indirectly heated walls of the shell, the dry speed of raw material is quickened and uniform drying efficiency is raised too. A well designed sealing system enable maintenance of deep vacuum inside the shell, and also ensures positive circulation of a heating media in the jacket.
Salient Features:
- Design is cGMP – Current Good Manufacturing Practices compliance
- All Product contact parts AISI 316/ 316L & non contact parts AISI 304.
- Simple & compact Design for Easy to operate, clean, convenient & user friendly.
- Automated mixing and Drying process in single bowl.
- Dust free operation.
- High vacuum operation
- Low temperature drying.
- Solvent recovery
- Continuous rotation of container, material will make complex impacting motion in the container and reach to uniform mixing and drying at low temperature..
- Continues vacuum maintenance during process.
- Vacuumized closed system with condenser, Receiver for solvent recovery & Cyclone separator to recovery the solid particle.
- Rapid & Complete discharge / Zero holdup after discharge
- The product dried is homogeneous with uniform properties.
- Very low value of final moisture even at low drying temperatures.
- Inside Filter assembly with 5 Micron.
MILLING AND SIZE REDUCTION
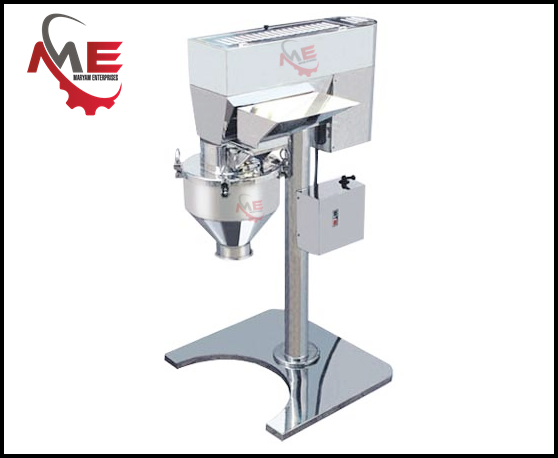
MULTI MILL
MARYAM ENTERPRISES is a leading and well known manufacturer of Multi Mill, is used for wet and dry granulation, pulverization, milling, shredding, chopping, size reduction in Pharmaceuticals, Chemicals, Cosmetics, Ceramics, Colors, Dyestuff, Food products etc. It also finds application in Pesticides, Fertilizers, Spices, Detergents, Insecticides, Plastics and Resins industries
In multi mill particle size reduction is done through impact in air, on material by blades moving at high speeds, inside a cylindrical sieve. The particles of the desired size pass out through the screen placed inside the hopper.
Salient Features:
- Design is cGMP – Current Good Manufacturing Practices compliance
- All Product contact parts AISI 316 & non contact parts AISI 304
- High speed milling, granulating, pulverizing, mixing and size reduction of wet & dry material.
- Output capacity 50 Kg to 200 Kg per hour..
- Easy removable contact parts for cleaning & inspection.
- Easy Mobility.
- Variable force by swing better having knife & impact edges are rotating within screen.
- Direction of beaters can be changed by forward- reversible switch.
- Various combinations of perforated sieves & wire mesh.
Optional Features:
- AC frequency drive for variable speed.
- Belt less Drive
- Inline milling process with HSMG and Sifter
- Flame Proof electrical.
- Safety Features :
- Over load protection.
MODEL | PMTM |
Output Speed | 50 Kg to 200 Kg Depends on products, speed and sieve size |
Rotor Speed | 750/1500/2300/3000 RPM by step pulley Option for VFD |
Rotor Diameter | 250 mm |
Charging Height | 1445 mm. |
Discharging Height | 730 mm. |
Motor | 3 HP/2.25 Kw/3 Phase/1440 RPM/AC |
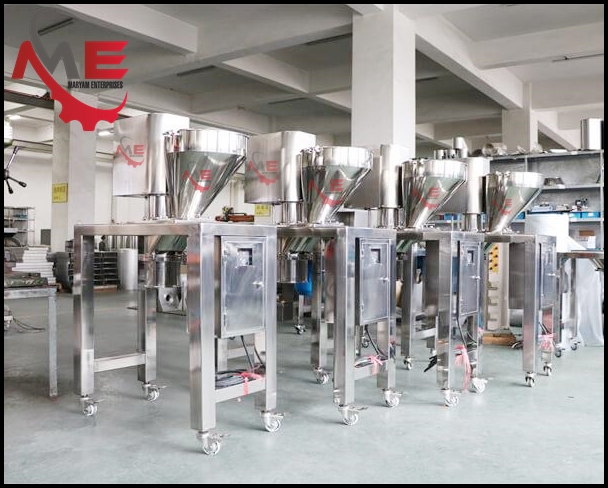
CONE MILL
MARYAM ENTERPRISES is a leading and well known manufacturer of Cone mill,is used for achieving de-lumping, dispersion, De agglomeration, fine grinding, dry and wet milling uniform size reduction, sieving and mixing in the pharmaceutical, food, fine chemical, personal care and cosmetics industries.
The product is poured into the feed hopper of the Cone Mill. In the conical screen chamber, a rotating impeller imparts a vortex flow pattern to the in feed product. The product is forced outward to the screen surface by centrifugal acceleration, ensuring continuous delivery into the “action zone” between the screen and impeller. No heating of product during granulation / sizing operation, due to better air circulation and lesser impact action. In the “action zone” the material is uniformly sized and instantaneously passed tangentially through the screen openings. The finished product is discharged at the bottom of the milling chamber.
Salient Features:
- Design is cGMP – Current Good Manufacturing Practices compliance
- All Product contact parts AISI 316/ 316L & non contact parts AISI 304.
- High speed milling, granulating, mixing and size reduction.
- Available in three model with different capacity for production scale.
- Uniform size reduction of wet material.
- Cone blade with cone type sieve for size reduction..
- AC frequency variable speed 100 to 1400 RPM.
- Easy removable contact parts for cleaning, inspection and easy Mobility.
- Various combinations of perforated sieves.
SIEVING – GRADING
VIBRO SIFTER
MARYAM ENTERPRISES is a leading and well known manufacturer of Vibro Sifter, is used for screening, sieving, grading for solid-liquid separation, process to separate the desired elements and the undesired elements from the combination of solid to solid (where two solids are generally having different properties) and solid to liquid material. It used in various industries such as Pharmaceutical, Chemicals, Cosmetics, plastics, paints, plastic, minerals, rubber compounds, metal powders, detergents, pesticides and fertilizers, dyestuff and pigments
Vibro sifter consists of a screen placed on the base plate attached centrally to gyratory motor. The material fed through the inlet located on the top is dropped on the screen. The particles smaller than the mesh size passes from the screen and the larger sized particles are released through an outlet. The combination of vibratory motor and the weights placed on top and bottom of screen gives the desired filtration or separation of the material. Total assembly is mounted on suitable springs so that it becomes an independent body which vibrates without parting any vibrations to the foundations.
Salient Features:
- Design is cGMP – Current Good Manufacturing Practices compliance.
- All contact parts AISI 316 & non contact parts AISI 304.
- Powerful vibration by gyratory motion by special Vibro motor.
- Side outlet & fines discharge.
- Easy movable & clean.
- Noiseless operation.
- Lead free and Silicon seal sieve.
FILTRATION
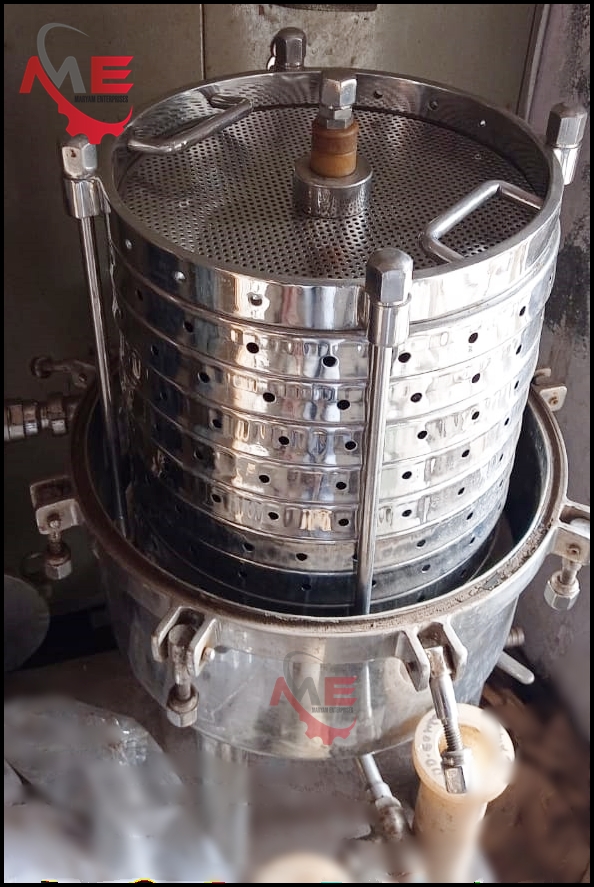
SPARKLER FILTER PRESS (FILTER PRESS)
MARYAM ENTERPRISES is a leading and well known manufacturer of Sparkler Filter Press, is a filtration machine used to filter liquid in pharmaceutical, chemical, beverage, and other industries. Filter Press works on the principle of pressure feeding.
Sparkler Filter Press is considered the most efficient filtration machine due to its significant properties.
It has a substantial flowrate with quality output. Liquid flows through the center rod then persuasively drawn to numbers of filter pads and filter plates. In this process, impurities are removed and stored in the form of compressed cake.
Salient Features:
- Due to the reverse flow of liquid, there is zero hold up in the filter press that leads to complete filtration of the batch.
- A backwash can provide a facility for continuous operations.
- No scavenger arrangement is required.
- The cake, filter aid & solids remain enclosed, allowing filtration of toxic, hazardous & explosive liquids.
- The top dome structure ensures fast & easy removal of cartridge assembly & cleaning of cake.
- We can increase the number of plates as per toxic levels of input or filtration requirements.
CENTRIFUGE
MARYAM ENTERPRISES is a leading and well known manufacturer of Centrifuge ,is efficient machine for Liquid Solid separation and centrifugal filtration/ fluid clarification in various industries such as Pharmaceutical, Bulk Drugs, API, Chemical, Textile, Herbal, Oil & Sugar Industries.
The centrifuge is a simple device usually driven by a motor that woks on the principle of sedimentation. Objects in a centrifuge are rotated around a fixed axis, thus applying a force perpendicular to the axis. The sedimentation principle uses the centripetal acceleration to evenly separate substances of varying density. Centrifuges can be divided or categorized on several bases such as manual top discharge, Lifting bag type and reversing filter bags with 3 point or 4 Point suspension and front charging & Pusher type.
Salient Features:
- Design is cGMP with all contact parts AISI 316.
- Centrifuge is used for separating liquids from solids and centrifugal filtration/ fluid clarification.
- It is offered in basket sizes of 24″ 36″ 48″ & 60″.
- Centrifuges offered in different model
- Heavy duty three point or four point suspension with under driven baskets.
- Front loading & discharge with horizontal driven basket.
- Pusher type centrifuge.
- These machines are available with top discharge, bottom discharge or bag lifting type.
- Filter cloth is available in the desired strength and micron size.
- The fabric with poly- propylene, woven / non woven polyester, nylon, cotton etc.
NUTSCHE FILTER
MARYAM ENTERPRISES is a leading and well known manufacturer of nutsche filters, We offer efficient nutsche filters for liquid / solid separation in a completely non-metallic environment. The entire unit is mounted on four legs with castor wheel for easy mobility. Our Nutsche Filter provides superior corrosion resistance and permits the handling of virtually all acids and salts at a very high temperature. The filter surface eliminates contamination to increase product purity and allows an easy, fast and thorough cleaning.
SHELL & TUBE HEAT EXCHANGER
MARYAM ENTERPRISES is a leading and well known manufacturer of Shell and tube heat exchanger in their various construction are probably the most widespread and commonly used basic heat exchanger configuration in the process industries. The reasons for this general acceptance are several. The shell and tube heat exchanger provides a comparatively large ratio of heat transfer area to volume and weight. It provides this surface in a form which is relatively easy to construct in a wide range of sizes and which is mechanically rugged enough to withstand normal shop fabrication stresses, shipping and field erection stresses, and normal operation conditions. There are many modifications of the basic configuration, which can be used to solve special problems. The shell and tube heat exchanger can reasonably easily clean, and those components most subjects to failure – gasket and tubes – can be easily replaced. Finally, good design method exists, and the expertise and shop facilities for the successful design and construction of shell and tube heat exchanger are available. Different no. of passes can also be given depending on the size and requirement of the Heat exchanger.
CONVENTIONAL COATING : PAN
Size: 24″/30″/36″/42″/48″/60″
MARYAM ENTERPRISES is a leading and well known manufacturer of Conventional coating machine, are used to sugar coat tablets, pills, etc in for a variety of industries such as Pharmaceutical, Confectionery, Food and others. They are also used for rolling and heating beans and edible nuts or seeds.
The product is to be filled inside the pan. During the rotation motion, coating material is sprayed by spraying system according to the technological process and rational technological process. So process materials (product) are coated due to rotating pan. The coating round pot is rotated by variable speed. At the same time hot air is supplied through inbuilt Hot air blower system which dries rapidly (heating or cooling) and evenly thus forming a solid and smooth surface.
Salient Features:
- Design is cGMP – Current Good Manufacturing Practices compliance.
- All contact parts AISI 316/304 & non contact parts AISI 304.
- Conventional coating system for manual film coating and sugar coating.
- Machine is designed with fabricated structure fitted with SS enclosure which makes simple, cleanable outside covering and mounted on anti vibration pad.
- Closed powerful pan drive with reduction gearbox and motor by variable speed pulley.
- Movable hot air blowing system with electric heater.
- Easy to replace polishing pan and other size coating pan.
Optional Features:
- A.C. frequency Drive for pan.
- Fixed or detachable type baffles.
- Interchange different size Pan & Polishing Pan
- Atomized Spraying system with Spray Gun, Peristaltic Pump and Solution tank and Electro Pneumatic controls.
- Pressurized vessel with spray gun.
- Flame Proof Electrical.
- Pellegrini type Coating machine.
OINTMENT / CREAM / TOOTH PASTE / GEL MANUFACTURING PLANT
MARYAM ENTERPRISES is a leading and well known manufacturer of Semi solid manufacturing Plants ,are ideal tools for the pharmaceutical & cosmetic industries for the production of Ointment, Cream, Lotion, Gel, Tooth Paste & emulsions & homogenization.
- Fully automatic Ointment, Cream, Tooth Paste , Gel manufacturing plant consisting of
- Pre determined water phase vessel.
- Pre determined oil, wax, petroleum jelly phase vessel.
- Vacuum Homogenizer Mixer vessel.
- Vacuum Pump
- Storage vessel
- Interconnecting pipeline.
- Transfer Pumps (Bump Pump, Lobe Pump & Metering pumps)
- Integrated automatic control panel.
- Working Platform
Design Features :
- Design compliance with cGMP
- Integrated Cleaning in Place-CIP.
- Sterilizing In Place-SIP as an Option.
- Batch Size
- Available model 50 Liter to 5000 Liter working Capacity.
Materials
- Product Contact AISI 316L.
- Food Grade silicon rubber for seal.
- Water Phase Vessel
- Jacket for heating & cooling.
- Heating Jacket Pressure (4 bar).
- Heating by steam or hot water circulation.
- Propeller stirring with top mounting.
- Temperature controller & safety pressure Valve.
- Bottom discharge with valve.
- Wax Phase Vessel
- Jacket for heating & cooling.
- Heating Jacket Pressure (4 bar).
- Heating by steam or hot water circulation.
- Propeller stirring with top mounting.
- Temperature controller & safety pressure Valve.
- Bottom discharge with valve.
- Manufacturing Vacuumize Homogenizer Vessel.
- Jacket for heating & cooling.
- Vacuumize process.
- Vessel Inside Pressure (-1 /+2 Bar)
- Heating Jacket Pressure (-1 /+6 bar)
- Heating by steam or hot water circulation.
- Agitator mixer with self pressure Teflon scrapper.
- Scrapper cleanly working on both side.
- High speed Homogenizer with toothed Rotor – stator type.
- RPM sleeplessly with variable speed drive for agitator & Homogenizer.
- High shear & pressurization of the homogenizer.
- Thus homogenization of high viscosities up to 400.000 mPas.
- Homogenizer mounted on lower position in the centre of vessel.
- Top lid with motorized top lid for lifting & lowering.
- Safety Interlock process with limit switch.
- Connection for Vacuum, Charging, Eye glass window, Light glass, CIP,SIP, Pressure gauge & safety valve.
- Temperature controller & safety pressure Valve.
- Bottom discharge with valve.
- Vacuum System
- Water Ring Vacuum Pump.
- Vacuum gauge & Vacuum relief valve.
- Storage Vessel
- Skid type storage vessel.
- Bottom cone is Jacket for heating.
- Inter Connecting Pipe
- Inter connecting Pipe line of all vessel for transfer Water, Wax & products.
- Re-circulation in manufacturing vessels.
- Vacuum connecting pipe.
- Working Platform
- Rigid structure with anti slipping embossed plat.
- Made from AISI 304.
- Controls & Visualization
- Electric Controls with digital display.
- Optional PLC Controls with HMI Touch screen.
- RPM and Process time entries.
- Temperature controls- Heat/cool.
- Vacuum start- Stop.
- Integrated Data Recording for batch.
- Safety Features
- Emergency stop button
- Safety vacuum relief valve & Indicator Gauge.
- Safety Pressure Valve.
- Limit switch at top lid.
LIQUID SYRUP MANUFACTURING PLANT
MARYAM ENTERPRISES is a leading and well known manufacturer of Liquid Syrup Manufacturing Plant
Detail
Preparation Vessels & Tank :
- Extremely hygienic processing.
- Least manual handling.
- Design compliance with cGMP
- Capacity up to 10,000 Liter.
- Product Contact AISI 316L
- Atmospheric, Vacuum or Pressure Operation.
- Jacket for heating & cooling.
- Vessel Inside Pressure (-1 /+2 Bar)
- Heating Jacket Pressure (-1 /+6 bar)
- Heating by steam or hot water circulation.
- Thermal Insulated.
- Mechanicals or Electro polishing of internal surface.
- Welded, flanged or hinged type cover
- Integrated Cleaning in Place-CIP.
- Sterilizing In Place-SIP as an Option.
- Portable execution on request.
- Validation protocols & Instrumentation celebration.
Variable Speed Agitation :
- Agitator can be top or bottom driven or magnetically driven.
- Propeller type, Anchor type provided with High speed disperser or rotor-stator homogenizer.
- Single or double mechanical seal.
Fully automatic Liquid Syrup Manufacturing Plant consisting of :
- Sugar Charging / Transfer System.
- Sugar Melting Vessel with mixing stirrer.
- Basket Filter & Transfer Pump.
- Syrup Manufacturing Vessel with stirrer.
- Inline Homogenizer.
- Zero Hold up Filter press.
- Storage Tank with stirrer.
- Interconnecting pipeline.
- Transfer Pumps.
- Integrated automatic control panel.
- Working Platform.
Turn Key Process Line :
- For production, filtration, transfer and storage solution.
- Pre reparation vessels.
- Inline homogenizer.
- Inter Connecting Pipe
- Solid or sugar Charging System
- Working Platform.
Automation available, appropriate for the intended process function, including CIP and SIP :
- Controls of all function by PLC Controls with HMI Touch screen.
- Level controls by means of capacitance probe or electronic load cells.
- Digital indication and controls of all process parameters for Process time, agitator speed, temperature, pressure & level.
RECEIVER
MARYAM ENTERPRISES is a leading and well known manufacturer of Stainless Steel Receivers and complete Pharmaceutical Plants and Pharmaceutical Plant Machinery manufacturer in India. SS Receivers are used in industries to store solvents. These receivers are generally been used in industries like chemical, pharmaceutical, Herbal, food processing biotechnology etc.
REACTION VESSEL
MARYAM ENTERPRISES is a leading and well known manufacturer of Reaction vessel, are used in Herbal Extraction Plant, Pharmaceutical plant and chemical plants for any chemical changes and process of reaction. We offer a wide range of reaction vessel at highly competitive prices, according to our client requirement. These Reaction vessels are highly efficient and durable
SOLVENT STORAGE TANK
MARYAM ENTERPRISES is a leading and well known manufacturer of storage tanks, are containers used for storage of gas, oil, water, and petrochemical products, employed for industrial uses. Industrial storage tanks come in different sizes and shapes. They can be underground, horizontal, and vertical.
SCREW CONVEYOR
MARYAM ENTERPRISES is a leading and well known manufacturer of Screw Conveyor, is to push material as the screw rotates in a fixed trough, pipe or housing. Using rotating helical screw blades (also referred to as flights or augers), screw conveyors appear in almost every industry and transport all types of materials.