Chemical Plants & Equipment
PLANETARY MIXER
The Planetary mixer machine is basically mixing assembly wherein the agitation pattern is of a planetary nature. If offers optimum output as these are installed with gearbox, variable speeds with electronic control.
Further, MARYAM ENTERPRISES can be customized as required by our clients. The blade movement and up-down movement is done through hydraulic system, so that electrical contact is avoided. CCTV is provided to see the operation in remote working PLC along with SCADA operates the full system from a safe distance.
For the processing of sensitive & hazardous heterogeneous compositions containing low to medium viscosity resins/binders & various dried particulate fillers having different particle size ( less than 1 micron to 300 micron) under high vacuum. Intimate mixing of these ingredients is must to ensure uniform mix. End of Mix viscosity to these compositions may vary from 50 poises to 80000 poises at 25°C. For removal of moisture & occluded gas / air from high viscosity composition, application of high vacuum of 0.1 mm of Hg is necessary during mixing. For very viscous compositions initial circulation of hot water through mixer jacket is essential and to avoid sudden rise in viscosity after addition of curing agents cold water circulation through jacket is required. The Planetary mixer unit consist of a Mixer, bowl with trolley, hydraulic drive unit, remotely operated control system with PLC & SCADA along with power back up system for PLC & close circuit camera & color Monitor for remote viewing, during Mixer Operation.
MARYAM ENTERPRISES offer wide range of planetary mixers for Defense industry which are manufactured in different specifications and capacities. With excellent deaeration, these planetary mixers prevent the paste from becoming lumpy. With robust construction and durability, these planetary mixers are widely used for mixing, degassing and kneading viscous and heat sensitive pastes. We also offer tailor made requirements. The speed of planetary mixers ranges from 1rpm to 100 rpm. We can obtain products containing solids Upto 85% in the final mixture.
Material of Construction (MOC) Offered : –
CS (IS 2062 Gr A/B, SA 516 Gr 60/70, BQ), SS 316, SS 304, SS 316 L, SS 304 L. SS 310, MONEL, INCONEL, TITANIUM, HASTALLOY, ETC.
REACTOR
Chemical reactors are vessels designed to contain chemical reactions. One example is a pressure reactor. The design of a chemical reactor deals with multiple aspects of chemical engineering. Chemical engineers design reactors to maximize net present value for the given reaction.
Designers ensure that the reaction proceeds with the highest efficiency towards the desired output product, producing the highest yield of product while requiring the least amount of money to purchase and operate. Normal operating expenses include energy input, energy removal, raw material costs, labor, etc. Energy changes can come in the form of heating or cooling, pumping to increase pressure, frictional pressure loss (such as pressure drop across a 90° elbow or an orifice plate), agitation, etc.
A) JACKETED REACTOR
in Conventional Jackets second shell is installed over a portion of the vessel, creating an annular space within which cooling or heating medium flows. A simple conventional jacket, with no internal components, is generally very inefficient for heat transfer because the flow media has an extremely low velocity resulting in a low heat transfer coefficient. Condensing media, such as steam or Dowtherm A, is an exception because in this case the heat transfer coefficient doesn’t depend on velocity or turbulence, but instead is related to the surface area upon which the media condenses and the efficiency of removing condensate. Internals include baffles that direct flow in a spiral pattern around the jacket, and agitating nozzles that cause high turbulence at the point where the fluid is introduced into the jacket
B) LIMPETED REACTOR
Limpeted Vessel with Closed Rigid Container is made using graded carbon steel and stainless steel alloy to ensure fine finish and long lasting usage. The Limpeted Vessel is equipped with closed rigid container for effectively holding gases and liquids at different pressure. The Limpeted Vessel is available in a sturdy construction that is easy to operate. Limpeted Vessel with Closed Rigid Container comes in varied shapes and sizes to cater to industrial requirement. PROCESS REACTION VESSEL
MARYAM ENTERPRISES have Multipurpose process reaction vessel, industrial reaction vessel and plants for manufacture of Bulk Drugs and APIs are designed keeping into consideration the various Process Parameters, also including clean-ability & product impurity profile. Based on these data, we analyze the Heat Transfer requirements, Degree of Agitation, Pressure – Temperature Ratings, Space Availability, Surface Finish requirements, Product Properties, HAZOP Studies, Corrosion Allowance etc., to offer an optimum system suiting your application.
MARYAM ENTERPRISES offer following things :
- Offered complete GMP systems with Basic & Process Engineering, Layout & Detail Engineering.
- Also meeting ‘C-GMP’ Standards and stringent requirements of International regulatory bodies like USFDA etc.
- Designed in accordance with the various international codes for Pressure parts.
- Internal surface finish’ up to 600 Grits with Mechanical / Electro-polishing having Crevice-free Internals to avoid contamination and facilitate thorough cleaning during product changeovers.
- Condenser vapor side is removable to facilitate manual cleaning.
- Pre – insulation for hot and cold service with SS304 cladding.
- Specially designed sealing mechanisms for bearing housing to prevent grease leakage even in a solvent atmosphere .
- Offered Italian Helical gearbox having high efficiency and reputed Mechanical Seal to prevent frequent seal failure resulting in oil leakages, also available with oil leakage collection chamber .
- Offered with various types of agitators such as Anchor, Turbine, MIG, Hydrofoil, Propeller, Helical and Contra mixer etc.
- The Vessel, Receiver, Column & Condensers with bolted openings can be dismantled to facilitate manual cleaning periodically or between product changeovers.
- The Nozzle & the Reflux line connections can be provided with Sanitary Triclamp, DIN, SMS, IDF or flange ends as specified by the user.
Material of Construction (MOC) Offered : –
CS (IS 2062 Gr A/B, SA 516 Gr 60/70, BQ), SS 316, SS 304, SS 316 L, SS 304 L. SS 310, MONEL, INCONEL, TITANIUM, HASTALLOY, PP/FRP ETC.
HEAT EXCHANGER
A) SHELL & TUBE HEAT EXCHANGER
Shell and tube heat exchanger in their various construction are probably the most widespread and commonly used basic heat exchanger configuration in the process industries. The reasons for this general acceptance are several. The shell and tube heat exchanger provides a comparatively large ratio of heat transfer area to volume and weight. It provides this surface in a form which is relatively easy to construct in a wide range of sizes and which is mechanically rugged enough to withstand normal shop fabrication stresses, shipping and field erection stresses, and normal operation conditions. There are many modifications of the basic configuration, which can be used to solve special problems. The shell and tube heat exchanger can reasonably easily clean, and those components most subjects to failure – gasket and tubes – can be easily replaced. Finally, good design method exists, and the expertise and shop facilities for the successful design and construction of shell and tube heat exchanger are available. Different no. of passes can also be given depending on the size and requirement of the Heat exchanger.
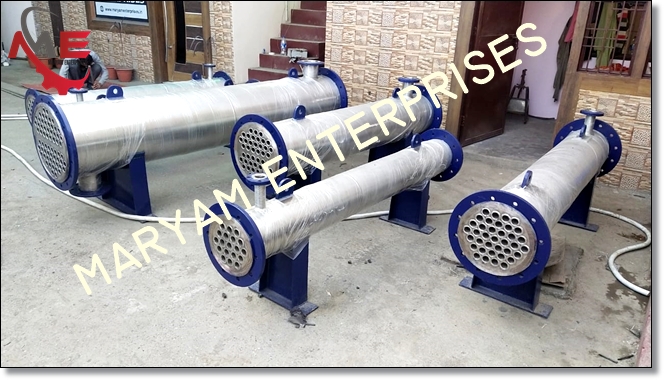
B) U-TUBE HEAT EXCHANGER
The U-tube head (U) is a very simple design requiring a bundle of U tubes, only one tube sheet, no expansion joints, and no rear-end head at all, allowing easy removal of the bundle. The thermal stress problem is eliminated because each tube is free to expand/contract independently. One disadvantage is, individual tube replacement is not possible except in the outer rows, and an even number of tube passes is required. Some tubes are lost in the center due to HEAT EXCHANGERS 17.7 tube bend limit, and tube side mechanical cleaning of the bends is difficult. Flow-induced vibration could be a problem for tubes in the outermost row. It is the lowest-cost design because there is no need for the second tube sheet.
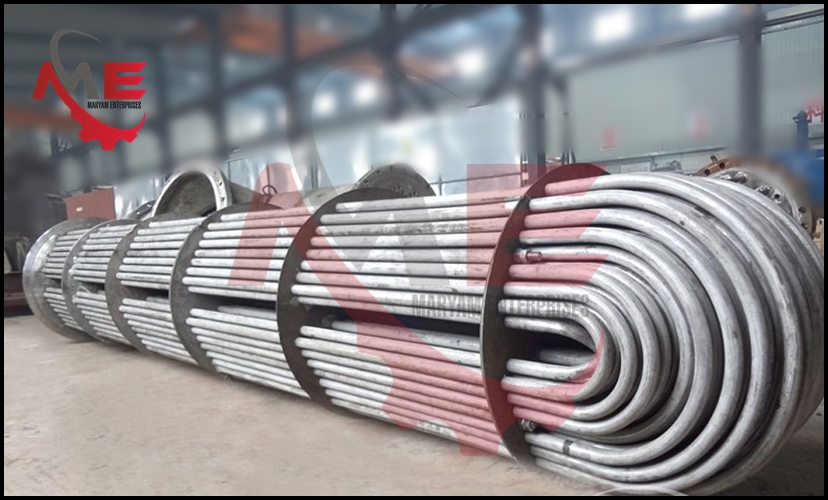
C) DOUBLE PIPE HEAT EXCHANGER
Double pipe heat exchangers are the simplest exchangers used in industries. On one hand, these heat exchangers are cheap for both design and maintenance, making them a good choice for small industries. But on the other hand, low efficiency of them beside high space occupied for such exchangers in large scales, has led modern industries to use more efficient heat exchanger like shell and tube or other ones. But yet, since double pipe heat exchangers are simple, they are used to teach heat exchanger design basic to students and as the basic rules for modern and normal heat exchangers are the same, students can understand the design techniques much easier. To start the design of a double pipe heat exchanger, the first step is to calculate the heat duty of the heat exchanger. It must be noted that for easier design, it’s better to ignore heat loss in heat exchanger for primary design. The heat duty can be defined as the heat gained by cold fluid which is equal to the heat loss of the hot fluid.
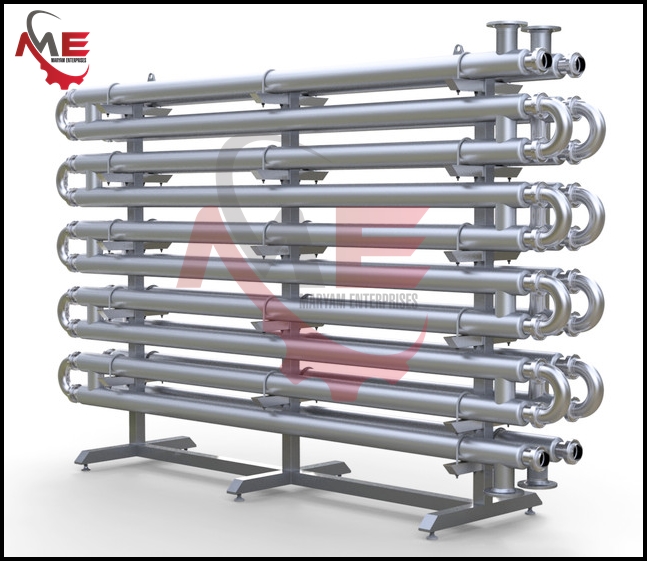
D) KETTLE REBOILER
Kettle reboilers are very simple and reliable. They may require pumping of the column bottoms liquid into the kettle, or there may be sufficient liquid head to deliver the liquid into the reboiler. In this reboiler type, steam flows through the tube bundle and exits as condensate. The liquid from the bottom of the tower, commonly called the bottoms, flows through the shell side. There is a retaining wall or overflow weir separating the tube bundle from the reboiler section where the residual reboiled liquid (called the bottoms product) is withdrawn, so that the tube bundle is kept covered with liquid and reduce the amount of low-boiling compounds in the bottoms product.
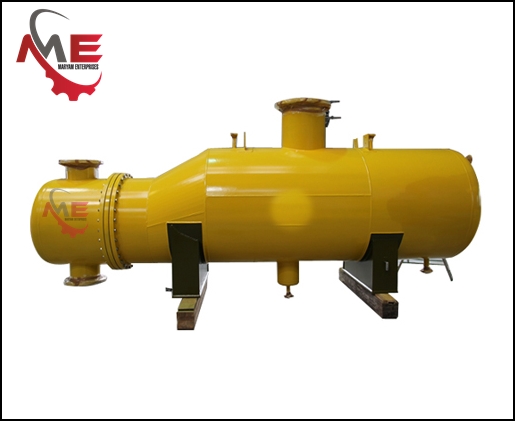
Material of Construction (MOC) Offered : –
CS (IS 2062 Gr A/B, SA 516 Gr 60/70, BQ), SS 316, SS 304, SS 316 L, SS 304 L. SS 310, MONEL, INCONEL, TITANIUM, HASTALLOY, ETC.
E) PLATE HEAT EXCHANGER
Another type of heat exchanger is the plate heat exchanger. One is composed of multiple, thin, slightly separated plates that have very large surface areas and fluid flow passages for heat transfer. This stacked-plate arrangement can be more effective, in a given space, than the shell and tube heat exchanger. Advances in gasket and brazing technology have made the plate-type heat exchanger increasingly practical. In HVAC applications, large heat exchangers of this type are called plate-and-frame; when used in open loops, these heat exchangers are normally of the gasket type to allow periodic disassembly, cleaning, and inspection. There are many types of permanently bonded plate heat exchangers, such as dip-brazed, vacuum-brazed, and c plate varieties, and they are often specified for closed-loop applications such as refrigeration. Plate heat exchangers also differ in the types of plates that are used, and in the configurations of those plates. Some plates may be stamped with “chevron”, dimpled, or other patterns, where others may have machined fins and/or grooves.
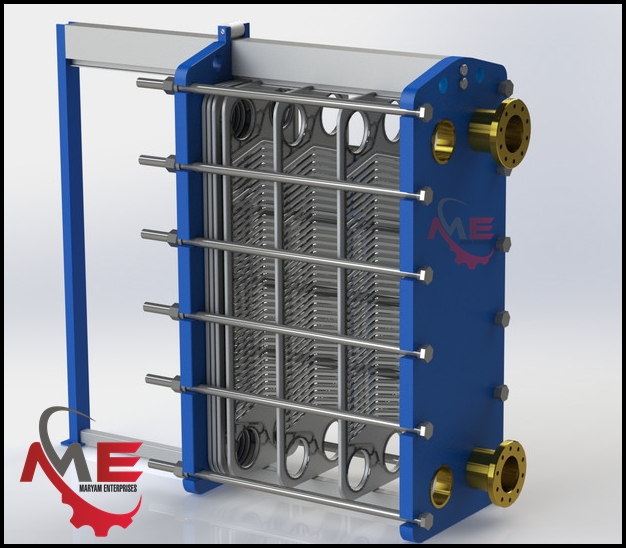
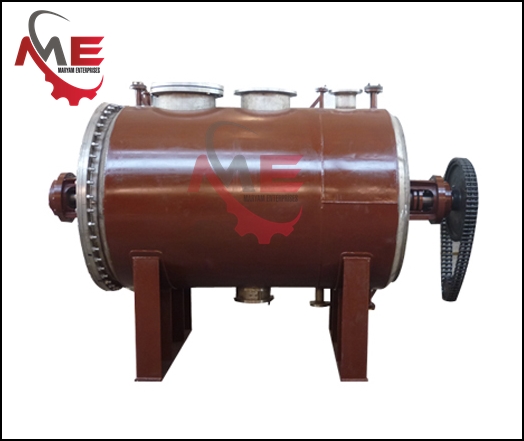
ROTARY VACUUM DRYER
The drying in a Rotary vacuum dryer is a batch operation under vacuum. It is possible to dry heat sensitive materials at well below boiling points of water and solvents. Drying time depends on material being dried, amount of solvent or water to be removed, desired final moisture content, permissible jacket temperature etc. The dryer is available in sizes ranging from 100 liters to 20,000 liters gross volume. The volume of wet material loaded into the dryer is usually restricted to 40-45% of gross volume.
Salient Features
- Equipped with different designs of agitators depending on the material to be dried.
- Unique quick opening discharge valve permits direct packing of dry product into bags or drums. Breaker rods are provided to prevent lump formation and allow quick and complete drying.
- Shaft sealing by mechanical seals is also available.
- N2 pulse jet dust filter (self cleaning type).
Rotary vacuum dryer has some typical applications in pharmaceuticals, organic chemicals, pasty materials, insecticides, pesticides, solvent recovery, dye intermediates, dyestuffs and in others industries.
Material of Construction (MOC) Offered : –
CS (IS 2062 Gr A/B, SA 516 Gr 60/70, BQ), SS 316, SS 304, SS 316 L, SS 304 L. SS 310, MONEL, INCONEL, TITANIUM, HASTALLOY, PP/FRP ETC.
FILTER
- Nutsche Filter
- Pressure sand Filter
- Activated Carbon Filter
- Sponge micro filter
(A) NUTSCHE FILTER
MARYAM ENTERPRISES is a leading and well known manufacturer of Nutsche Filters and complete Chemical Plants and Chemical Plant Machinery manufacturer in India. Nutsche Filter is a closed vessel designed to separate solid and liquid by filtration under pressure or vacuum.
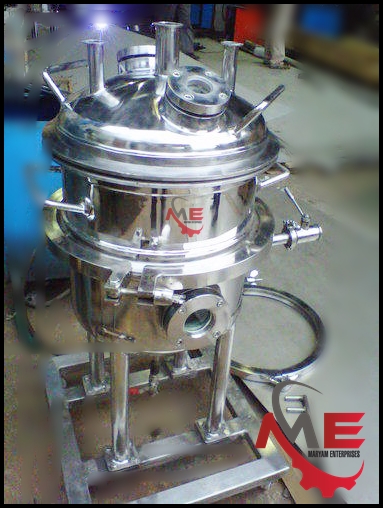
(B) PRESSURE SAND FILTER
Pressure sand filter is used for the removal of suspended solids & turbidity. The pressure sand filter is extremely robust method of removing suspended solids from water. The filtration medium comprises of multiple layers of sand having different sizes. As per the needs of our customers, we can offer sand filters in various sizes and material apart from hand operated or fully automatically operated.
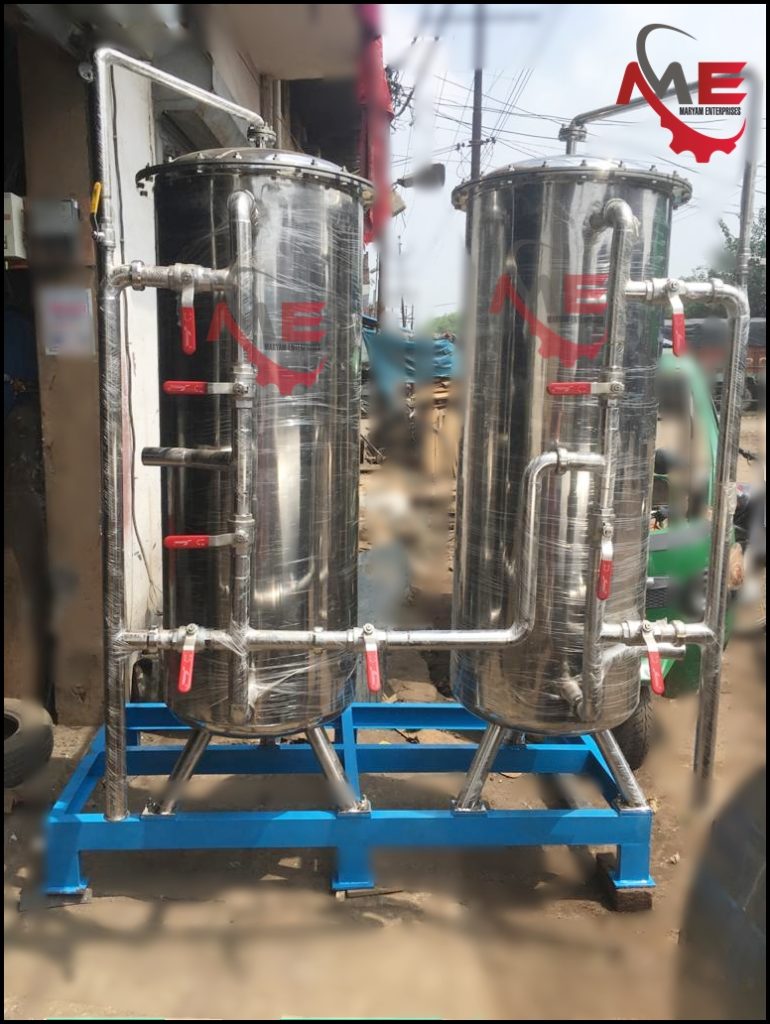
HOW IT WORKS?
- 1. Raw water is passed through sand filter at a pressure of 2 – 3.5 kg / cm2.This reduces the suspended solids that are present in the raw water.) Nutsche Filter
- We offer efficient nutsche filters for liquid / solid separation in a completely non-metallic environment. The entire unit is mounted on four legs with castor wheel for easy mobility. Our Nutsche Filter provides superior corrosion resistance and permits the handling of virtually all acids and salts at a very high temperature. The filter surface eliminates contamination to increase product purity and allows an easy, fast and thorough cleaning.
- 2. This filter has the ability to remove up to 30 to 50 micron of suspended solids to less than 5 ppm
- 3. It is mandatory to wash the filter daily with raw water for 20 to 30 minutes
- 4. For the filtration of partials below 30 to 50 micron, the cartridge filter is used
- 5. They are manufactured in mild steel, stainless steel, FRP, MS/RL etc.
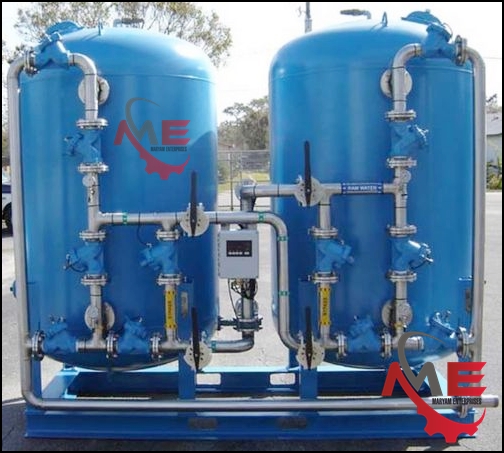
(C) ACTIVATED CARBON FILTER
The Activated Carbon Filters are manufactured in MS / SS / FRP / MS/RL etc. They contain a perforated plate at bottom with layers of Activated Carbon. When the fluid passes through the Activated carbon bed, the odor / smell is retained by the carbon and odorless fluid passes through. When the carbon bed gets saturated, it is replaced with new one.
The Activated Carbon Filter finds applications in
- Pharmaceutical industry
- Dairy & food products
- Beverages
- Package drinking water
- Cosmetics
- Thermal power plants
- Agriculture etc.
(D) SPONGE MICRO FILTER
The air pump pushes air through the tubing into the hollow cavity inside the sponge filter. Bubbles rise from the inside of the sponge, thus drawing water through the sponge walls. This water suction process mechanically collects debris from the aquarium and gives beneficial bacteria place to grow.
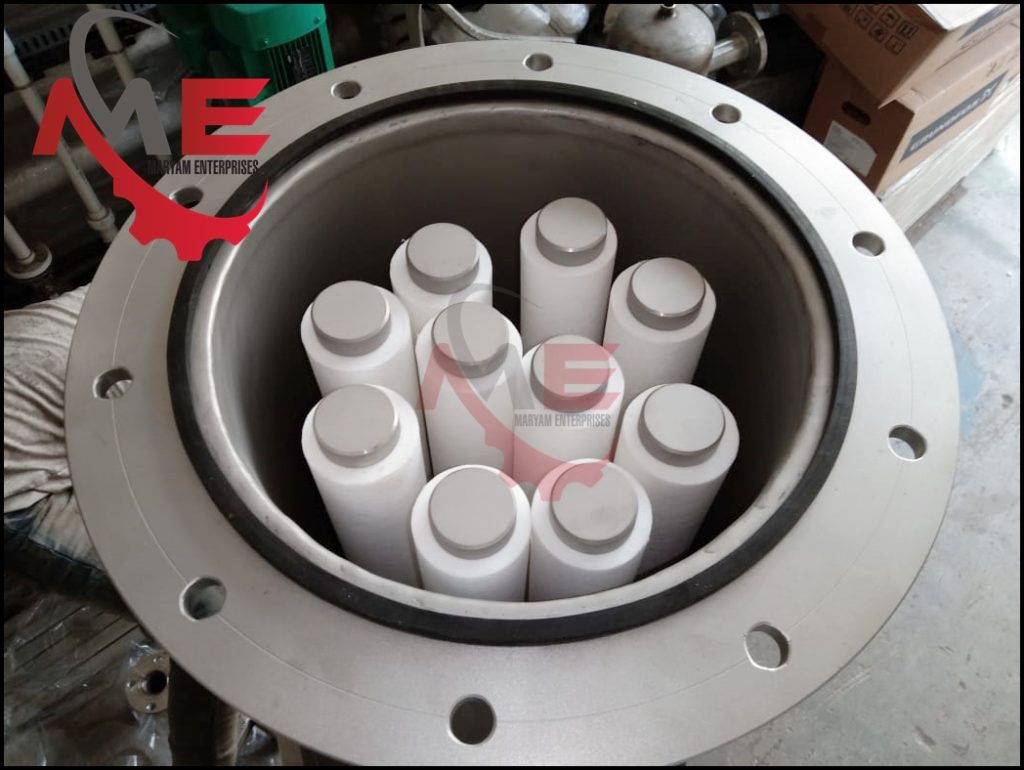
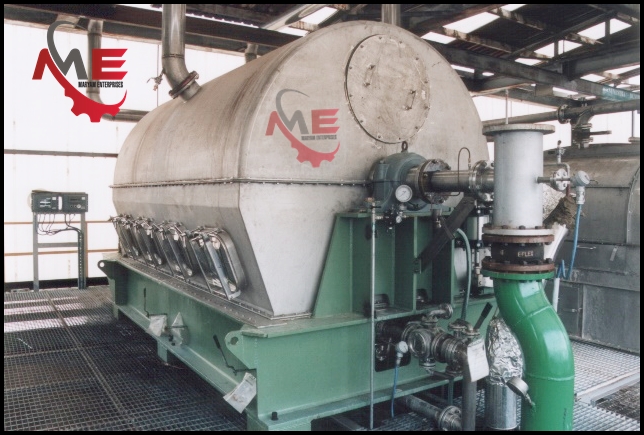
Drum Flakers:
Flakers are used for solidifying molten material. After processing on flakers, the material forms films or easily handled flakes and is further processed or packed into containers for transport. A great advantage of flakers is that they offer a continuous process. The hot material is applied to the cooling drum by direct immersion into a trough, or indirect immersion using doctor/applicator rolls. The molten liquid is cooled on the cooling drum and after a partial revolution; the cooled and solidified product is removed by a scraper in the form of flakes or film.
Special Features :
- Designed for trouble free operation
- Low Cost operation
- Continuous Process
- High thermal efficiency
- Minimum thermal degradation
- Accomplishment of flaking in a single step
- Uniformly flaked product
We manufacture, design and develop optimum quality rotary drum flakers. Our range of drum flakers is available in single drum flakers, double drum flakers.
Material of Construction (MOC) Offered :-
CS (IS 2062 Gr A/B, SA 516 Gr 60/70, BQ), SS 316, SS 304, SS 316 L, SS 304 L. SS 310, MONEL, INCONEL, TITANIUM, HASTALLOY, PP/FRP ETC.
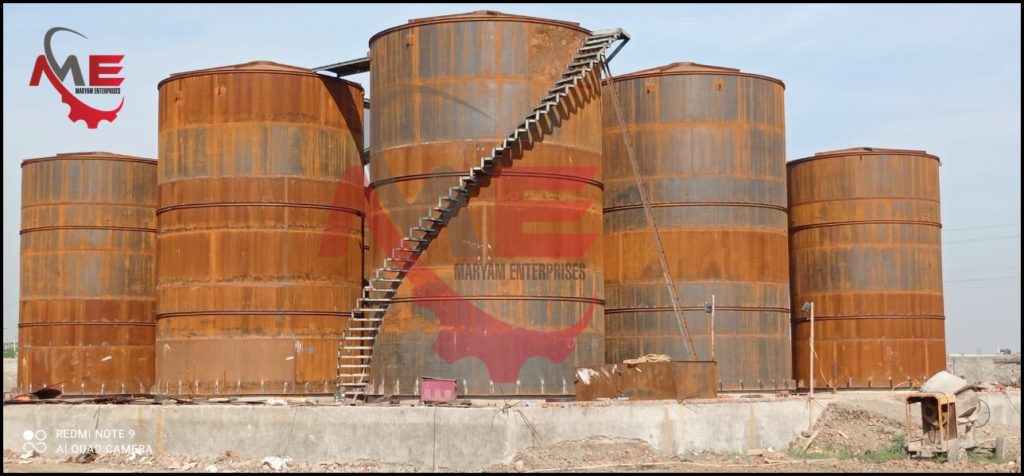
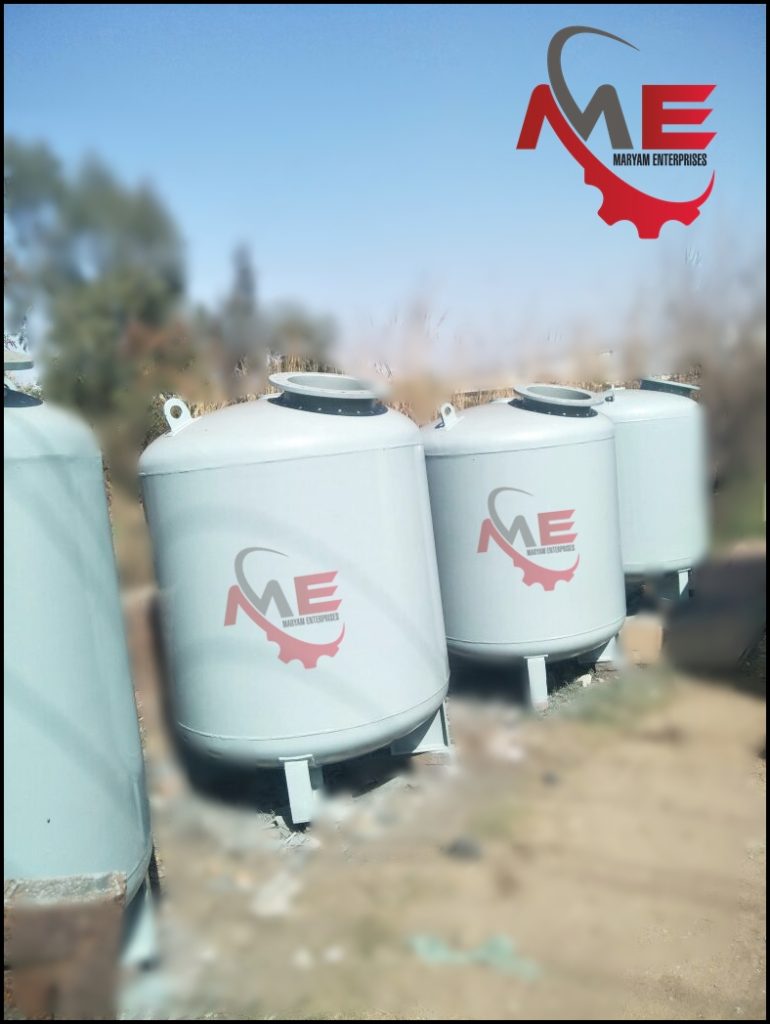
STORAGE TANK
We provide full customization on our storage tanks as per the specifications and requirements of the client. All the raw materials are used depending on usage of the tank and also as per client’s input. These tanks are corrosion resistant and easily withstand various temperature fluctuations and variations. These tanks have a wide demand in various processing industries because of them being highly qualitative at cost effective prices.
We are manufacturing and supplying a highly functional range of storage tanks that find wide application in process industries. These storage tanks are used in many configurations depending upon their functional requirements such as operating temperature and storage medium.
These storage tanks are offered to our clients in the following shapes:
- Horizontal Storage Tanks
- Vertical Storage Tanks
- Elliptical Shaped Storage Tanks
- Dished Shaped Storage Tanks
- Flat Storage Tanks
- Conical Head Storage Tanks
MARYAM ENTERPRISES hold expertise in offering SS Storage Tanks for meeting the process demands of chemical industry. We use various material of construction such as MS, Boiler Quality Plates, Stainless Steels, Alloy Steels, Aluminum, MS/Lead bonded & FRP.
SCRUBBERS
Scrubber systems are a diverse group of air pollution control devices that can be used to remove some particulates and/or gases from industrial exhaust streams. Traditionally, the term “scrubber” has referred to pollution control devices that use liquid to wash unwanted pollutants from a gas stream. Recently, the term is also used to describe systems that inject a dry reagent or slurry into a dirty exhaust stream to “wash out” acid gases. Scrubbers are one of the primary devices that control gaseous emissions, especially acid gases. Scrubbers can also be used for heat recovery from hot gases by flue gas condensation.
Types:
- Packed Bad Scrubber
- Plate Type Scrubber
- Cyclonic Scrubber
- Venturi Scrubber
- Wet Scrubber
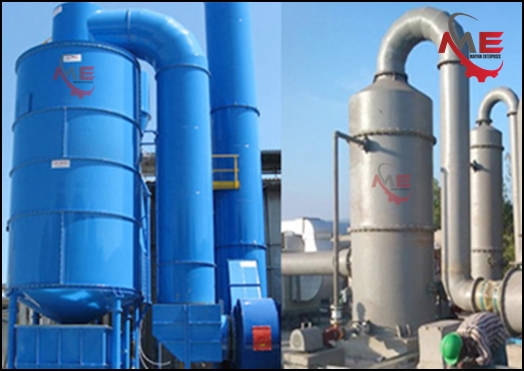
Material of Construction (MOC) Offered:-
CS (IS 2062 Gr A/B, SA 516 Gr 60/70, BQ), SS 316, SS 304, SS 316 L, SS 304 L. SS 310, MONEL, INCONEL, TITANIUM, HASTALLOY, PP/FRP ETC.
RIBBON BLENDER
Ribbon Blenders are very sturdy and robust. They consist of a U type Vessel with flat head. The central agitator shaft is driven from end with gear box reducer. A double helical ribbon agitator in the vessel moves the product upward along the outer wall and releases it downward into cavities developed in the middle, simultaneously material is horizontally distributed by the mixing arm and is optimally homogenized.
Mixing time is depending on the agitator speed. In general mixing time is three to four times shorter than the mixers working with a rotating screw. The S.S. RIBBON BLENDER is an efficient and versatile blending machine for mixing of dry granules & powders homogeneously.
The dry material gets sufficient continuous movement due to the shape & movement of ribbon & shape of the container, which moves material for good quality of blending.
The unit consists of one electrical motor, one worm reduction gear, belt drive between motor and gear, couple drive between gears to (ribbon) mixing stirrer. Container having four numbers of legs with discharge valve & top cover. Both ends of mixing shaft are sealed with bush & stuffing box.
DESIGN OPTION:
- Models with single or double helix.
- Net capacities for 20 to 25000 liters.
- Various Material and surface treatment available depending upon product characteristics.
- Liquid adding by ISP system.
- Heating Cooling jackets with insulation.
MARYAM ENTERPRISES provide ribbon blenders that give a triple mixing action for efficient blending. Great emphasis is laid on its dimension and configuration for quick product discharge.
Its distinguishing features are:
- Wear resistance
- Corrosion Resistance
- Vacuum filling and discharge arrangements
- Special shaft seals
- Heating & cooling jackets
EVAPORATORS
• FALLING FILM EVAPORATOR
A FALLING FILM EVAPORATOR is an industrial device to concentrate solutions, especially with heat sensitive components. The evaporator is a special type of heat exchanger.
Due to the intimate contact of the liquid with the heating surface, these evaporators are sensitive to fouling from precipitating solids; liquor velocity, typically low at liquor inlet (see above) is usually not sufficient to perform an effective self-cleaning of the tubes. Falling film evaporators are therefore used in clean, non-precipitating liquids. A typical application, in chemical industry, is for concentration of caustic soda.
• RISING FILM EVAPORATOR
A RISING FILM or VERTICAL LONG TUBE EVAPORATOR is a type of evaporator that is essentially a vertical shell and tube heat exchanger. The liquid being evaporated is fed from the bottom into long tubes and heated with steam condensing on the outside of the tube from the shell side. This is to produces steam and vapor within the tube bringing the liquid inside to a boil. The vapor produced then presses the liquid against the walls of the tubes and causes the ascending force of this liquid. As more vapor is formed, the centre of the tube will have a higher velocity which forces the remaining liquid against the tube wall forming a thin film which moves upwards. This phenomenon of the rising film gives the evaporator its name.
There is a wide range of applications for rising tube evaporators, including effluent treatment, production of polymers, food production, thermal desalination, pharmaceuticals, and solvent recovery.[2] In terms of applications within these industries, rising tube evaporators are mainly used as reboilers for distillation columns, or as pre-concentrators or flash evaporators or pre-heaters designed to remove volatile components prior to stripping.
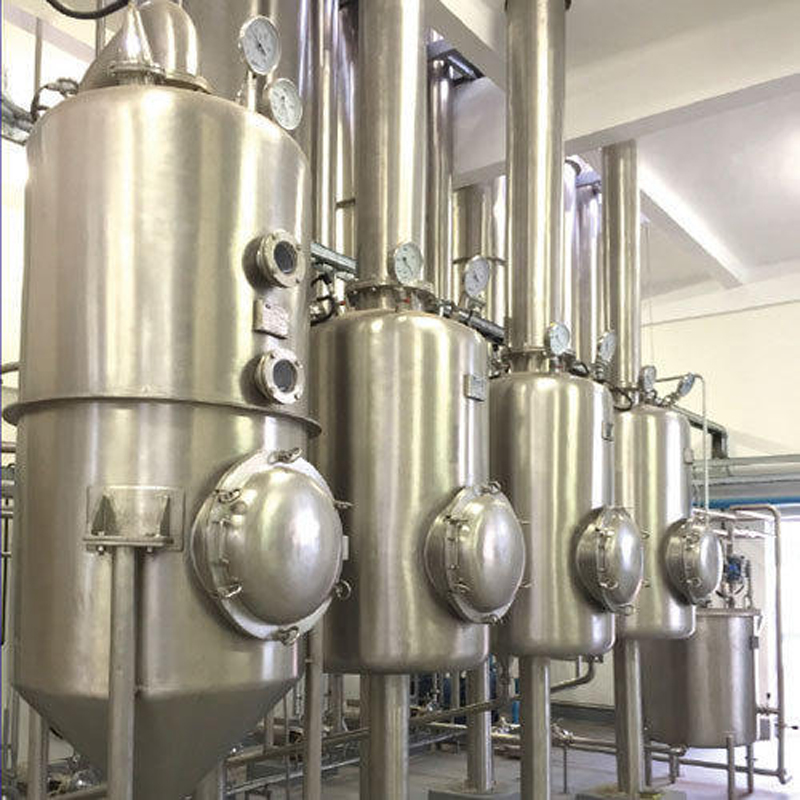
• MULTIPLE EFFECT EVAPORATORS
MULTIPLE-EFFECT EVAPORATOR, as defined in chemical engineering, is an apparatus for efficiently using the heat from steam to evaporate water. In a multiple-effect evaporator, water is boiled in a sequence of vessels, each held at a lower pressure than the last. Because the boiling temperature of water decreases as pressure decreases, the vapor boiled off in one vessel can be used to heat the next, and only the first vessel (at the highest pressure) requires an external source of heat. While in theory, evaporators may be built with an arbitrarily large number of stages, evaporators with more than four stages are rarely practical except in systems where the liquor is the desired product such as in chemical recovery systems where up to seven effects are used.
Material of Construction (MOC) Offered: –
CS (IS 2062 Gr A/B, SA 516 Gr 60/70, BQ), SS 316, SS 304, SS 316 L, SS 304 L. SS 310, MONEL, INCONEL, TITANIUM, HASTALLOY, ETC.
DISTILLATION COLUMN
A DISTILLATION COLUMN is an essential item used in distillation of liquid mixtures so as to separate the mixture into its component parts, or fractions, based on the differences in volatilities. Fractionating columns are used in small scale laboratory distillations as well as for large-scale industrial distillations.
Material of Construction (MOC) Offered: –
CS (IS 2062 Gr A/B, SA 516 Gr 60/70, BQ), SS 316, SS 304, SS 316 L, SS 304 L. SS 310, MONEL, INCONEL, TITANIUM, HASTALLOY, ETC.
Packed Columns / Bed
In chemical processing, a PACKED BED is a hollow tube, pipe, or other vessel that is filled with a packing material. The packing can be randomly filled with small objects like Rasching rings or else it can be a specifically designed structured packing. Packed beds may also contain catalyst particles or adsorbents such as zeolite pellets, granular activated carbon, etc.
The purpose of a packed bed is typically to improve contact between two phases in a chemical or similar process. Packed beds can be used in a chemical reactor, a distillation process, or a scrubber, but packed beds have also been used to store heat in chemical plants. In this case, hot gases are allowed to escape through a vessel that is packed with a refractory material until the packing is hot. Air or other cool gas is then fed back to the plant through the hot bed, thereby pre-heating the air or gas feed.
Material of Construction (MOC) Offered : –
CS (IS 2062 Gr A/B, SA 516 Gr 60/70, BQ), SS 316, SS 304, SS 316 L, SS 304 L. SS 310, MONEL, INCONEL, TITANIUM, HASTALLOY, ETC.
FLAKERS
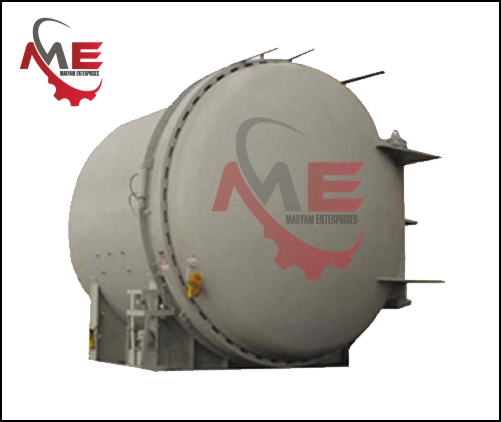
AUTOCLAVE
An AUTOCLAVE is a device used to sterilize equipment and supplies by subjecting them to high pressure saturated steam at 121°C for around 15–20 minutes depending on the size of the load and the contents.
Autoclaves are widely used in microbiology, medicine, podiatry, tattooing, piercing, veterinary, mycology, dentistry, and prosthetics fabrication. They vary in size and function depending on the media to be sterilized.
Typical loads include laboratory glassware, other equipment and waste, surgical instruments and medical waste.
Material of Construction (MOC) Offered : –
CS (IS 2062 Gr A/B, SA 516 Gr 60/70, BQ), SS 316, SS 304, SS 316 L, SS 304 L. SS 310, MONEL, INCONEL, TITANIUM, HASTALLOY, PP/FRP ETC.
ISO TANK
A tank container is built to the ISO Standard, making it suitable for different modes of transportation. Both hazardous and non-hazardous products can be transported in tank containers.
A tank container is a vessel of stainless steel surrounded by an insulation and protective layer of usually Polyurethane and aluminum. The vessel is in the middle of a steel frame. The frame is made according to ISO standards and is 19.8556 feet (6.05 meters) long, 7.874 feet (2.40 meters) wide and 7.874 feet (2.40 meters) or 8.374 feet (2.55 meters) high. The contents of the tank range from 27,000 to 40,000 liters (5,900 to 8,800 imp gal; 7,100 to 11,000 U.S. gal). There are both smaller and larger tank containers, which usually have a size different from the ISO standard sizes.
Material of Construction (MOC) Offered : –
CS (IS 2062 Gr A/B, SA 516 Gr 60/70, BQ), SS 316, SS 304, SS 316 L, SS 304 L. SS 310, MONEL, INCONEL, TITANIUM, HASTALLOY, PP/FRP ETC.
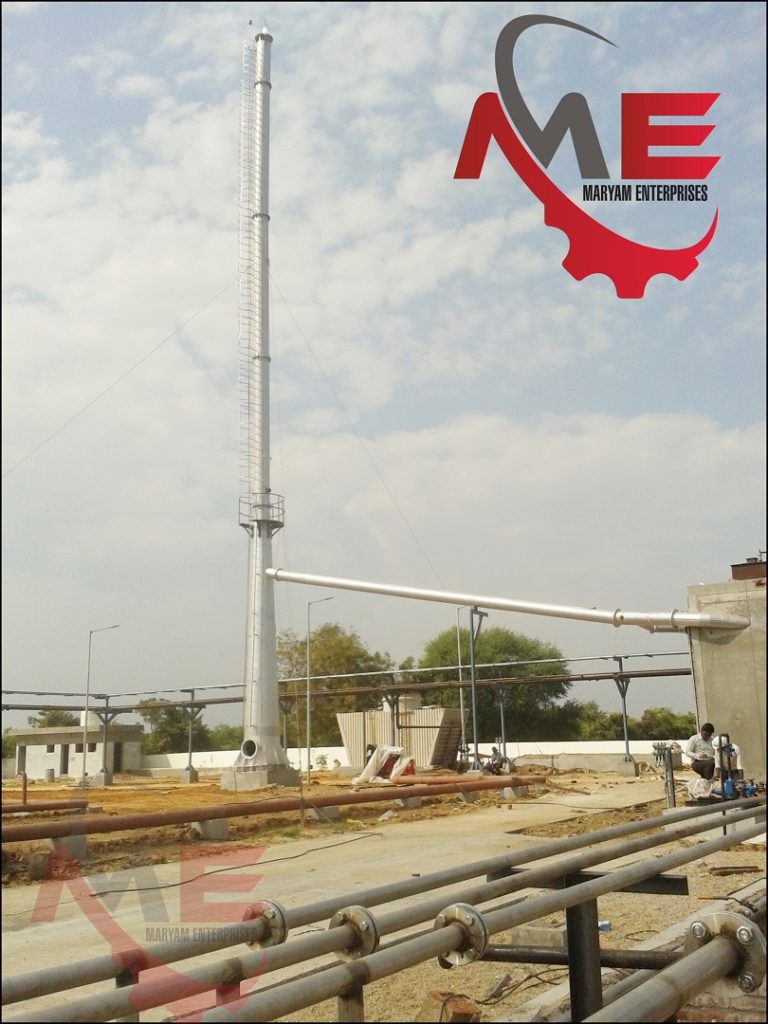
CHIMNEY
A Chimney is a structure which provides ventilation for hot flue gases or smoke from a boiler, stove, furnace or fireplace to the outside atmosphere. Chimneys are typically vertical, or as near as possible to vertical, to ensure that the gases flow smoothly, drawing air into the combustion in what is known as the stack, or chimney, effect. The space inside a chimney is called a flue. Chimneys may be found in buildings, steam locomotives and ships. In the United States, the term smokestack (colloquially, stack) is also used when referring to locomotive or ship chimneys, and the term funnel can also be used.
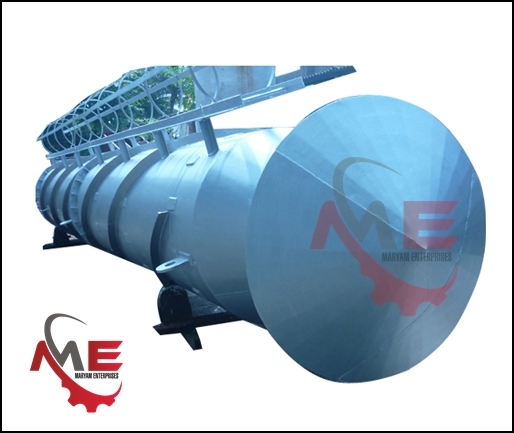
Material of Construction (MOC) Offered : –
CS (IS 2062 Gr A/B, SA 516 Gr 60/70, BQ), SS 316, SS 304, SS 316 L, SS 304 L ETC.
VIBRATORY FLUID BED DRYER
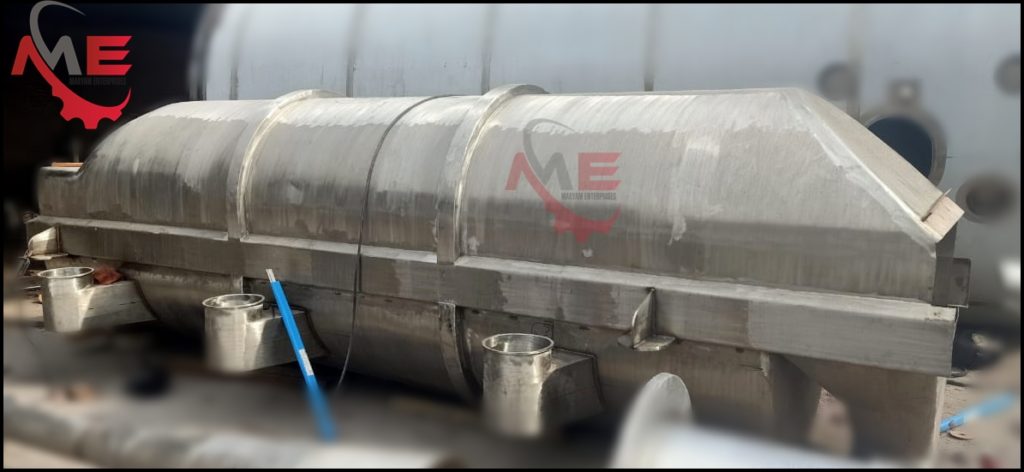
Vibratory Fluidized Bed (VFB) is another type of fluidized bed where the mechanical vibration, enhance the performance of fluidization process. Since the first discovery of vibratory fluidized bed, its vibration properties proves to be more efficient in dealing with fine particles which appears to be very difficult to achieve with normal fluidized bed. Even though numerous publications and its popularity in industrial applications, the knowledge about vibratory dynamics and properties are very limited. Future research and development are needed to further improve this technology to bring it to another level.
Standard type of vibratory fluidized dryer consist of vibrating tray conveyor where hot gases from the chamber will flow through the holes within the tray and come in contact with the materials to be dried. The tray area is big enough to tolerate constant flow of material through the bed and passed along the deck with a low depth on the tray. The vibrations to the deck are directed in vertical component to assist in fluidization of the material whereas the horizontal component of the vibration, support in transporting materials along the tray.
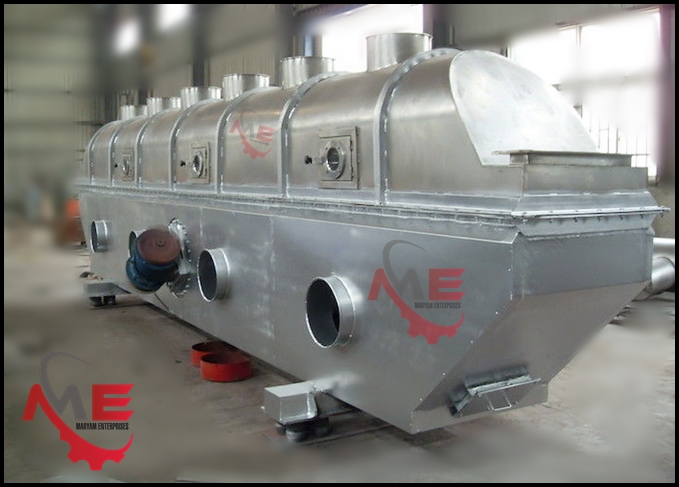
Some of the advantages of vibratory fluidized beds include:
- Continuous drying throughout the unit.
- Handle products with a wide range of particle size and shape.
- Minimal fluidization velocity and pressure drop due to the vibration energy being transferred along the bed.
- Increase efficiency of gas to solid contact.
- Mechanical vibration enhances homogeneity and stability of fluidized bed layers.
- Easier to control the residence time distribution of processed material by manipulating the intensity of amplitude and frequency of vibration.
- Limitations of vibratory fluidized bed are as follow
- The inlet air temperature to the dryer process is limited.
- Climate condition can affect the unit’s thermal efficiency.
- Build-up of local expansion region lead to unstable behavior to the bed structure.
Material of Construction (MOC) Offered : –
CS (IS 2062 Gr A/B, SA 516 Gr 60/70, BQ), SS 316, SS 304, SS 316 L, SS 304 L. SS 310, MONEL, INCONEL, TITANIUM, HASTALLOY ETC.